What is a ceramic film?
Release time:
May 17,2024
Author:
Source:
Ceramic film is a general term for oxidizing substances. The true ceramic film is composed of substances such as silicon dioxide and titanium nitride (TiN). The ceramic materials used in automotive films include tin oxide, indium oxide, tungsten oxide, etc. These materials have selective filtering function in the solar spectrum, lower reflection, better stability, and the characteristics of removing metal films without blocking signals.
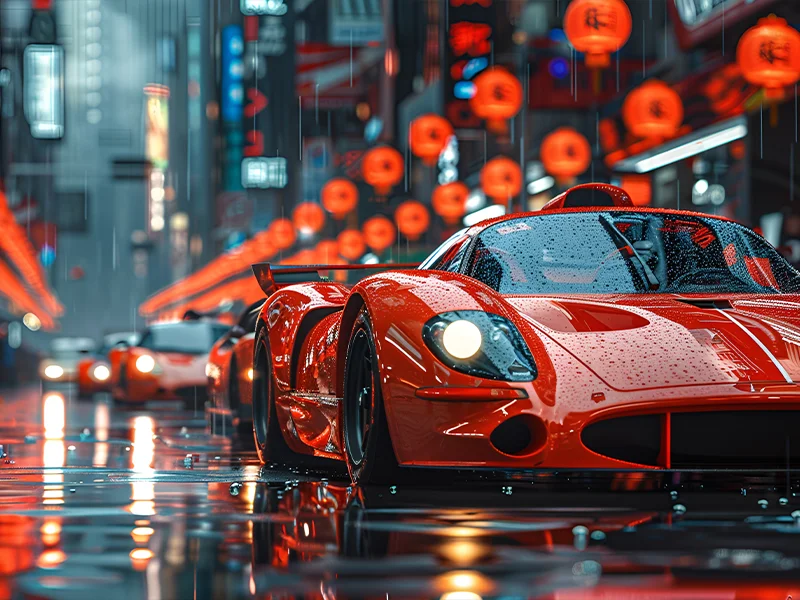
Ceramic film is a general term for oxidizing substances. The true ceramic film is composed of substances such as silicon dioxide and titanium nitride (TiN). The ceramic materials used in automotive films include tin oxide, indium oxide, tungsten oxide, etc. These materials have selective filtering function in the solar spectrum, lower reflection, better stability, and the characteristics of removing metal films without blocking signals. The insulation method of truly good top-level ceramic films is mainly based on barrier, and adding organic IR+absorbent will impersonate the ceramic film. This type of "ceramic film" is absorption and insulation, but in fact, these are two different products. Organic IR is highly prone to decomposition, and over time, its insulation function and color will decrease. A true ceramic film is theoretically permanent, and its stability cannot be compared to that of a metal film. The structure of ceramic membranes can be divided into three types based on the different carriers: flat plate, tube, and multi-channel. Due to its good resistance to acid and alkali, high temperature, and extreme environmental chemical stability, the filtration accuracy of ceramic membranes generally includes three types: microfiltration, ultrafiltration, and nanofiltration. These are ceramic membranes, they are real ceramic membranes.
The membrane may have one or more parallel flow channels that extend through the entire component of the porous support structure.
In order to achieve all the required effects of the ceramic film, specific coating materials need to be coated on the walls of all flow channels of the film. This special coating material contains silicon carbide, which is first dried and then sintered at high temperature in an inert atmosphere. This coating not only makes the membrane strong and durable, but also determines the flow channel aperture and water flux of the membrane. Learn more about membrane production processes and membrane coatings here.
Liquid filtration
Liquid filtration involves multiple processes. The pump ensures that the feed flow is under pressure from one end of the membrane, which will allow the liquid to flow through the channel of the membrane. The liquid flowing through the membrane barrier is called permeate. The permeate flows to the outer carrier of the membrane and is continuously discharged as a filtered liquid. Suspended solids, oil droplets, oil lotion, particles and bacteria cannot penetrate the barrier and are therefore rejected. All removed elements are called concentrates. The concentrated solution flows through the membrane channel and terminates at the other end of the membrane.
Membrane cleaning
When the liquid is filtered, visible and invisible objects in the feed water, such as particles, oil, and biomass, will eventually begin to contaminate the membrane. But through three cleaning procedures, complete scaling can be avoided. This cleaning process can be done manually, semi-automatic, or automatically.
The first process is cross flow, and due to the shear force on the membrane surface, the membrane is cleaned with water. This process is the most common scenario.
The second process is traditional backwashing. Backwashing is generated by a backwashing pump, which flushes water back in the opposite direction through the membrane hole.
The third process is in-situ chemical cleaning, abbreviated as CIP. In situ cleaning involves cleaning all membranes with chemicals, heat, and water, without the need to disassemble the water treatment unit. CIP is an effective method for quickly and effectively cleaning membranes, which is crucial in liquid filtration processes. An effective cleaning process ensures a shorter downtime for the entire water filtration system, providing more efficient and cost-effective operations. Read more information about how to clean ceramic membranes here.
Future Sustainable Development Standards
In addition to the above advantages and characteristics, ceramic membranes can also reduce energy consumption, reduce backwash water consumption, improve processing capacity, and occupy a small footprint. This ensures compliance with current and future environmental regulations, as well as more sustainable, efficient, and cost-effective operations. Therefore, ceramic membranes enable the development of other industries while meeting future sustainable development standards.
Latest developments
Selection and usage steps of window film
May 17,2024
How to identify automotive film
May 17,2024
Types of anti-counterfeiting labels and films
May 17,2024
Copyright ©2024 Guangzhou Broadya New Materials Manufacturing Co., Ltd |
| Powered by www.300.cn | Urban substation | SEO |